4 Log Water Treatment
Do You Meet 4 Log Water Treatment Requirements? Let Passaic Bergen Water Softening Help You Meet Compliance Monitoring Regulations
With Aqua Treatment Service’s cutting-edge equipment, the ATS 186K is now validated to meet or exceed the 4.0 Log reduction (LRV) or 99.99% water disinfection requirements as established by The EPA Guidance Manuals.
Experience
Aqua Treatment Service has over 30 years of experience in the water treatment industry. Key management personnel have worked with Federal, State, and Local Regulatory agencies in the design, specifications, and performance requirements of water treatment equipment.
Product Testing & Evaluation
The Aqua Treatment Service Multi-Barrier Drinking Water Disinfection System meets or exceeds the 4.0 Log removal (LRV) or 99.99% disinfection requirements as established by The EPA Guidance Manuals.
A full-scale Multi-Barrier System has been Evaluated and Performance Verified for Public and Private Water Supply Systems by the USEPA Testing and Evaluation Facility and 3rd party independently tested by Shaw Environmental in Cincinnati, Ohio, with analysis and results of Adenovirus testing by The USEPA National Exposure Research Laboratory (NERL) in Cincinnati, Ohio. The ATS-186K UV has been Independently 3rd Party Tested by Carollo Engineers, Idaho, to meet EPA Ultraviolet Disinfection Guidance Manual (UVDGM) 4 Log Virus reduction at >186mJ UV Dose.
Performance
The Multi-Barrier Filtration and Ultraviolet Disinfection System will provide a 4 Log Removal Value (LRV) in removing bacteria, Cryptosporidium oocysts, and Viruses, including Adenovirus in drinking water for use towards achieving log reduction credits for Federal and State Regulatory acceptance to meet the 4-log microbiological contaminates reduction requirements of The Long Term 2 Enhanced Surface Water Treatment Rule (LT2ESWTR) and Ground Water Rule (GWR), and Ground Water Under the Direct Influence of Surface Water (GUDI).
Public Water and Private Drinking Water, Make-up Water, Product Water, Process Water, Reclaim Water, Water Discharge Systems, Electronics, Semiconductor, Pharmaceutical, Medical Device, Biotech, Hospitals, Laboratories, Food Processing, Dairy, Liquid Syrups, Beverages, Bottled Water, Potable Water, Rain Water to Drinking Water and more.
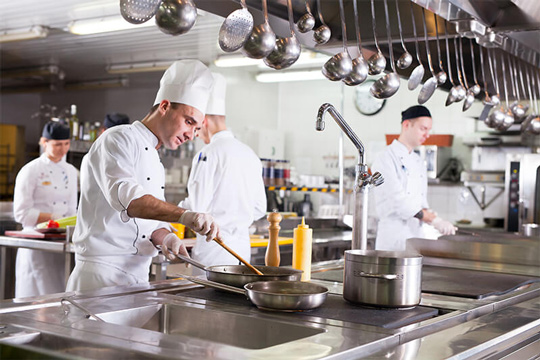
Chlorine vs SKMB Series
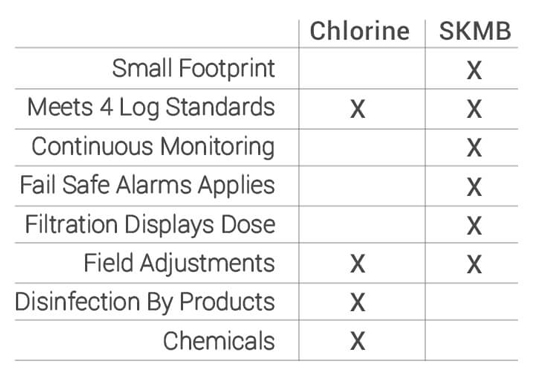
Chlorine Concerns:
- Chlorine Injection / Residual Level requirements vary from State to State.
- Chlorine required field adjustments for dosing levels, injection / residual level requirements change with water quality, water temperature, organic load and flow rates.
- Chlorine requires hazardous materials handling, storage, containment and training.
- Chlorine Does not Reduce all Bacteria, Cryptosporidium and Virus of concern.
- Chlorine contact tanks requires a large footprint for space.
- Chlorine inline Analyzers require additional chemical reagents to be handled and stored on site.
- Chlorine injection levels required for 4 Log disinfection may reach levels that require monitoring for DBP’s (Disinfection By Products)
The Limitations and Concerns Associated With Chlorine
Chlorine, a commonly used disinfectant in water treatment, has effectively eliminated harmful bacteria and viruses from our drinking water. However, growing concerns exist regarding its potential adverse effects on our health and the environment. Some studies suggest that chlorine disinfection can create harmful byproducts, such as trihalomethanes, that may increase cancer risk and the potential for other diseases. In addition, the use of chlorine in water treatment can also create an unpleasant taste and smell in the water, and its usage varies based on state and local guidelines as well. With the presence of 4 log water treatment, we must break down and address the concerns surrounding chlorine’s effectiveness and limitations and how ATS 186K can help to cover up these issues.
- Chlorine Injection / Residual Level requirements vary from State to State.
- Chlorine required field adjustments for dosing levels, injection / residual level requirements change with water quality, water temperature, organic load, and flow rates.
- Chlorine requires hazardous materials handling, storage, containment, and training.
- Chlorine Does not Reduce all Bacteria, Cryptosporidium, and Virus of concern.
- Chlorine contact tanks require a large footprint for space.
- Chlorine inline Analyzers require additional chemical reagents to be handled and stored on-site.
- Chlorine injection levels required for 4 Log disinfection may reach levels that require monitoring for DBPs (Disinfection Byproducts)
Our Engineering Department can provide complete equipment project design specifications, submittal, and drawing packages for all our SKMB-Series Models.
Aqua Treatment will provide site installation, Startup, and Operations Training on the Multi-Barrier System.
Aqua Treatment Service Inc. is a U.S.A.-based manufacturer. All Multi Barrier designs are engineered & produced at its Mechanicsburg, PA facility, from the Ultraviolet stainless steel chambers, Filtration stainless steel vessels, and electrical control panels to the plumbing and system layout for skids. State-of-the-art, unique programmable 5-axis laser stainless steel cutting system allows custom fabricated components and parts to the highest tolerances and quality control.
Waterline Technology, a U.S.A.-based manufacturer of Filtration Systems, partnered with Parker Hannifin Corporation to pleat its CMF Charged Membrane Filtration Cartridges with flow rates from 10-40 GPM per cartridge. Parker, a world leader in process filtration, produces CMF cartridges of the highest quality, and Waterline Technology’s Quality Control system requires a non-destructive performance test on each cartridge. The Dual O-Ring open one end outside end-patented design ensures all the processed raw water is directed to the cartridge(s). Waterline Technology also has partnered with Aqua Treatment Service to manufacture filter vessels to Waterline’s design exclusive sealing system specifications for the cartridges within the vessels.
Contact our Technical support team for assistance on our SKMB Series equipment operation, standard features, options, sizing factors, application criteria, and Model Series selection. We work with you from the initial design conception through the installation and startup process
Sales and Technical Support
Aqua Treatment Service Inc. is a U.S.A.-based manufacturer. All Multi Barrier designs are engineered & produced at its Mechanicsburg, PA facility, from the Ultraviolet stainless steel chambers, Filtration stainless steel vessels, and electrical control panels to the plumbing and system layout for skids. State-of-the-art, unique programmable 5-axis laser stainless steel cutting system allows custom fabricated components and parts to the highest tolerances and quality control.
Waterline Technology, a U.S.A.-based manufacturer of Filtration Systems, partnered with Parker Hannifin Corporation to pleat its CMF Charged Membrane Filtration Cartridges with flow rates from 10-40 GPM per cartridge. Parker, a world leader in process filtration, produces CMF cartridges of the highest quality, and Waterline Technology’s Quality Control system requires a non-destructive performance test on each cartridge. The Dual O-Ring open one end outside end-patented design ensures all the processed raw water is directed to the cartridge(s). Waterline Technology also has partnered with Aqua Treatment Service to manufacture filter vessels to Waterline’s design exclusive sealing system specifications for the cartridges within the vessels.
Contact our Technical support team for assistance on our SKMB Series equipment operation, standard features, options, sizing factors, application criteria, and Model Series selection. We work with you from the initial design conception through the installation and startup process.
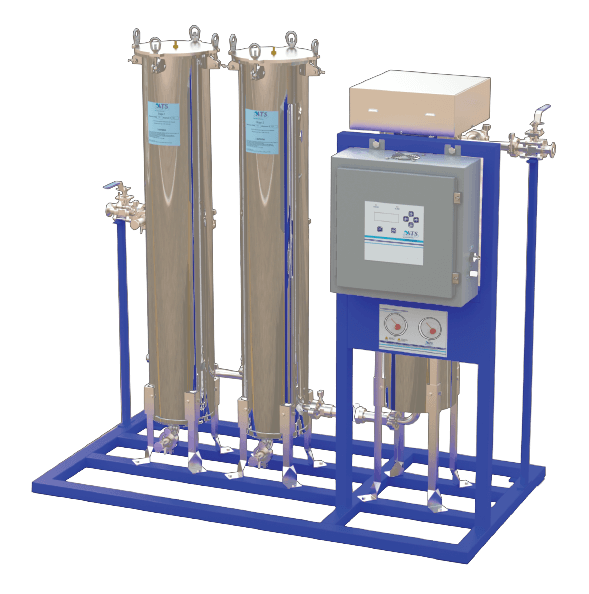
186,000 ws/cm2 (186mJ) UV Dose
- 304 Stainless Steel Filter Housings & UV Chamber
- NPT or flange inlet/outlet connections
- Filter Differential Pressure
- UV Lamp Status
- UV Monitor
- Temperature Overheat Control
- Powder-coated steel skids
- System Remote Control Logic Controller
- 120Volt/60Hz or 220Volt/50-60Hz
- Flow Meter
- ATS Microprocessor Controller
- LCD Display w/ Touch Pad Controls
- Audible and Visual Alarms
- Lamp Status – Hours, Expired
- Real-Time Display of Filter and UV Conditions
- Power and Ballast Operation Detection
- Data Log of Alarm History
- Technician Screen
- Ancillary equipment connections
Stage 1:
- PPF Spun Polypropylene 5 Micron high-efficiency Turbidity cartridge
- Sanitary Clamps for a quick change of cartridge
- Patented Exclusive Single O- ring cartridge Sealing System
- Pressure Differential Alarm
- Clean & Dirty Water Drain
- Stage 2:
- CMF™ Charged Membrane Filtration
- pleated cartridge
- Sanitary Clamps for a quick change of cartridge
- Clean & Dirty Water Drain fitting
Waterline Technology, a U.S.A.-based manufacturer of Filtration Systems, partnered with Parker Hannifin Corporation to pleat its CMF Charged Membrane Filtration Cartridges with flow rates from 10-40 GPM per cartridge. Parker, a world leader in process filtration, produces CMF cartridges of the highest quality, and Waterline Technology’s Quality Control system requires a non-destructive performance test on each cartridge. The Dual O-Ring open one end outside end-patented design ensures all the processed raw water is directed to the cartridge(s). Waterline Technology also has partnered with Aqua Treatment Service to manufacture filter vessels to Waterline’s design exclusive sealing system specifications for the cartridges within the vessels.
Contact our Technical support team for assistance on our SKMB Series equipment operation, standard features, options, sizing factors, application criteria, and Model Series selection. We work with you from the initial design conception through the installation and startup process
Stage3
- ATS-186K High Dose Ultraviolet Disinfection System
- 186,000uws/cm2 (186mJ) at the end of Lamp Life 12,000 Hours
- UV Intensity Monitor
- NIST Certified UV Sensor
- Validated UV Lamp Output
Log-reduction technology was developed to provide engineers with an easier way to explain biological contamination in water. 4 log reduction is the gold standard, with systems getting increasingly less valuable as that number decreases. Log utilizes the base-10 decimal system, in which log 10 is base 1, log 100 is base 2, log 1000 is base 3, etc.
The log reduction percentages are as follows:
- 1-log reduction removes 90% of bacteria.
- 2-log reduction removes 99% of bacteria.
- 3-log reduction removes 99.9% of bacteria.
- 4-log reduction removes 99.99% of bacteria.
There are very real reasons for applying the log system to public health sectors. For one, the EPA has found that the presence of pathogens in public and groundwater sources is a major concern. Illness and disease breakouts increase in likelihood because of this, with one of the most common being 12 waterborne outbreaks between 1984 and 1998. As such, the Interim Enhanced Surface Water Treatment Rule (IESWTR) set requirements to reduce the risk of Cryptosporidium and other harmful contaminants in any water distribution system serving at least 10,000 people.
4-log water treatment is critical. Groundwater systems are subject to tests if they do not already meet the minimum level of 4-log system protection. Via compliance monitoring, systems must show 4-log protection using chemical disinfection, membrane filtration, or any state-approved treatment technologies.
DEV: make these h2’s drop downs
186K 3 Stage Multi-Barrier Skid:
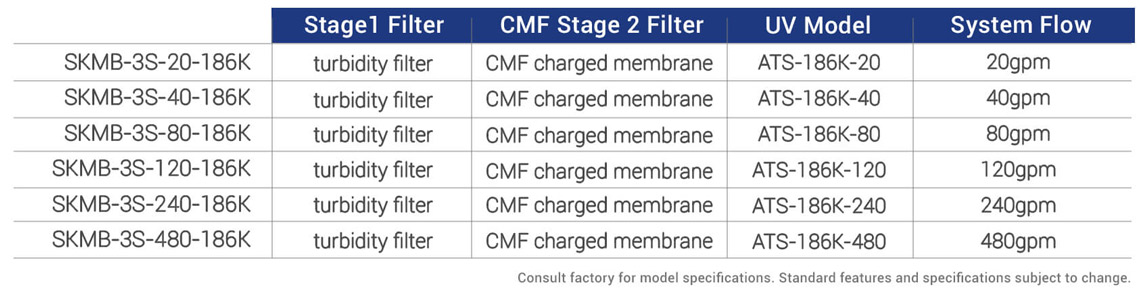